Pyrolysis is a process in which waste rubber is converted into fuel oil, by chemical decomposition , in the presence of heat and absence of oxygen. Pyrolysis, also known as thermal cracking or thermolysis, occurs at high temperatures. It is an irreversible process and the physical and chemical changes of the substance takes place simultaneously. The end products of the process are liquid oil, gaseous fractions and solid char.
Uses of Pyrolysis
Rubber is a high polymer which is hard to decompose naturally. If it is left on the surface of the earth or buried underground, it deteriorate for more than 10 years and will hardly decompose. The accumulation of unwanted rubber can pollute the environment and causes harm to human kind. It can catch fire easily, which is another reason, it should be decomposed properly. However, being a high polymer, it is a very valuable renewable source. The waste rubber pyrolysis plant helps in using rubber waste to produce various useful compounds. Waste rubber recycling by pyrolysis can reduce the black pollution. It is used to relieve energy crisis and generate profits. It uses highly advanced technology and is highly efficient. Both government and non government agencies can profit from these pyrolysis plants. There is no soil, air or water contamination. This process attains 100% waste rubber recycling.
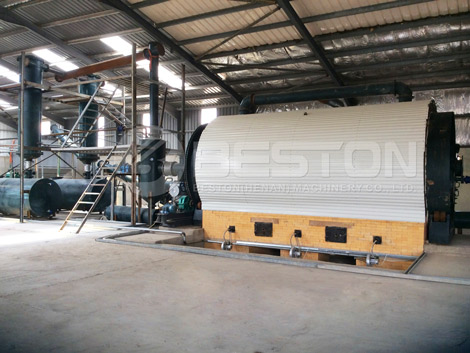
Final products of pyrolysis:
1. Fuel Oil
50%-75% of the end products is fuel oil. It is used in generation of electricity in heavy oil generators. It is also used in tractors, trucks, etc. It is also used as heating material in cement factory, steel making factory, electricity power factory and ceramic factory.
2. Carbon Black
30%-35% of the end products is Carbon Black, which is used a slag for construction. It is also used as carbon absorbent after further activation.
3. Flammable gas
8%-10% of the end products is flammable oil, which is further recycled into furnace. This is then used for heating thereactors. Click here to know more: https://bestonpyrolysisplant.com/.
1. Initially, the waste rubber is fed into the reactor with the help of auto-feeder or can also be done manually. The inlet door for feeding is then sealed in order to be sure that there is no leakage of gas.
2. Using char, charcoal or wood as heating materials, heat the reactor.The reactors starts getting heated slowly and oil gas will form when temperature reaches about 250 degree C.
3. The oil gases then condensed in the condensing system and are converted into liquid oil.
4. The gas which is not liquefied will go back to the combustion system through safety device. This gas can be recycled and used for heating the reactor. This can save the energy required for the whole process.
5. After the oil production, the reactor is cooled down to 40 degree C, where solid char is formed. This can be discharged either automatically or manually.
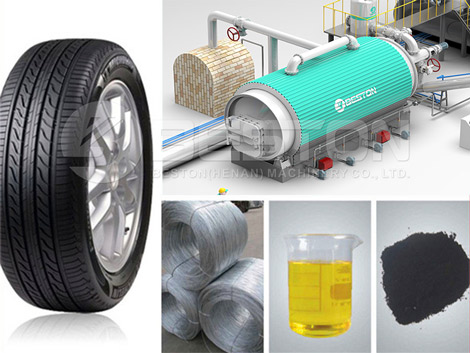
Pyrolysis process usually takes place for 4 hours to 12 hours, depending on the size of the plant, quantity of the waste rubber, nature of the waste rubber, etc.
It is one of the most cost effective way of reusing waste rubber. The oil yield of pyrolysis process depends on various parameters like the quantity and quality of raw material, condensation system of the plant that plays a vital role in converting the gases into oil, temperature, etc.
Pyrolysis Plant: Environment Friendly waste tyre pyrolysis plant usually causes to pollution or has no adverse effects on environment. A well operated pyrolysis plant, is usually clean and is more beneficial and causes no harm. It requires very little energy for the process, as it uses its own gas produced during the process to heat the reactor. In order to remove the ash and waste, it has a dedusting system. The whole pyrolysis is a sealed process, meaning there will be no leakage of gas or oil produced during the process. The solid char which is produced at the end of the process is discharged by the automatic discharging system, which means there will be no solid waste remained at the end that is undischarged.
The main pollution controlling equipment used in pyrolysis plants include exhaust gas scrubber, flue gas flaring system, oil water seperation system, spill proof carbon evacuation system, spill proof steel evacuation system, H2S rubber, fire hydrant line, gas analyzers, etc.
It can be said that the rubber waste pyrolysis plant proves to be more profitable and seems to have no significant drawbacks or negative effects on the environment.