A biomass pyrolysis equipment processes biomass raw materials such as bamboo, wood chips, coconut shell, sawdust, palm shell and plant straw into charcoal, wood vinegar, biogas and tar by using biomass pyrolysis plant. The main product is high caloric value charcoal which contains a high carbon content and is used as an alternative to traditional coal. The pyrolysis of biomass is done in an environment-conscious manner that safeguards the environment. Hence it is an ideal investment.
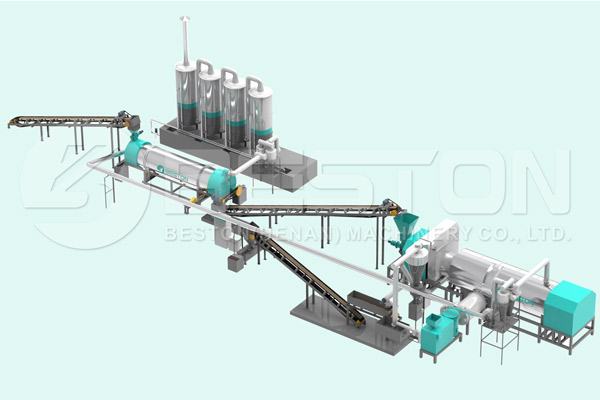
Components of Biomass Pyrolysis Equipment
The components of a rice husk carbonizer depend on its size and complexity. The main parts of the plant include: a pre-processing section that has equipment for chipping, drying, grinding and sieving raw materials, conveyor belts and storage bins for moving and handling materials, feeding equipment such as feed belts and lock hoppers and also a dryer where required. Other components are biochar kiln, gas purification chamber and quenching or cooling sections. The plant also has electrical components such as generators.
Raw Materials Used in A Biomass Pyrolysis Equipment?
Biomass includes a wide variety of materials such as weeds, sawdust, straw, leaves, bamboo, sugarcane bagasse, peanut shell, coconut shell, wood, palm shell and other forestry and agricultural waste. A lot of these materials can be acquired cheaply. This translates into lower input costs and hence higher profits for the biomass pyrolysis plant.
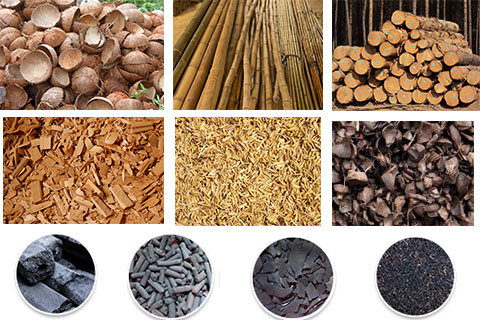
Production Process
Typically, the entire biomass process consists of four stages. They are; fast pyrolysis of materials at high temperature, smoke discharge, sulphur reduction and enriching the charcoal. First, the raw materials are subjected to moisture removal so that the residual moisture level is at 20% or lower. Then they are crushed into tiny pieces of 50mm or less.
The crushed materials are then moved by conveyor belts into the biochar pyrolysis reactor where they are heated. At the right temperature, the raw materials produce charcoal and combustible gas. This step takes approximately 15 minutes. Consequently, the charcoal is moved through a cooling chamber. The temperature is lowered to 30℃ which is conducive for direct discharge of the biomass charcoal.
The combustible gas produced in the furnace will be passed through the spay dedusting section and condenser chamber to get rid of sulphur elements and then extract tar. Finally, wood vinegar is extracted as the last product. The cleaned combustible gas is recycled by directing it through the draft fan equipment into the dryer or furnace. This ensures the whole production process is eco-friendly.
End Products from Biomass Pyrolysis Plant
The primary end product of the plant is biomass charcoal that is pollution-free and has a high caloric value. It is the preferred option for use in barbecues as well as for heating metals in the smelting industry. Also, it can be used in agriculture as an additive to natural fertilizer, to enhance soil integration and to improve the quality of the soil. For direct use, the charcoal can be produced into different shapes such as charcoal balls using forming equipment to add value and get a higher price for it. The other products produced are tar, combustible gas and wood vinegar. Click www.BestonMachinery.com/ for details.
Through the use of advanced carbonization technology a biomass pyrolysis equipment guarantees top quality products, efficiency in heat utilization and increased working efficiency. The entire production process is green ensuring that pollution of the environment is prevented.